Dear customer
Thank you very much for your interest in products and services of BQ+ Medical. In order to enable us to cooperate more efficiently, we have prepared a Frequent Question & Answer list as following:
BQ+ understands that your needs go beyond just purchasing medical device. Our engineers and technicians are very much experienced in medical device R&D, manufacturing and related regulatory compliance and government requirements. Working with BQ+ can reduce engineering, mold and equipment costs, as well as speed up your time to market.
If you don’t find items from BQ+ catalogue that exactly fits your application needs, our sales representatives and product development engineers will work closely with you to solve your most challenging problems. We are committed to helping you achieve the best economics and performance from your products and will assist you in meeting relevant certifications and government regulatory requirements.
BQ+ Medical Service
Q1May I download BQ+ Catalogue?
Ans
Catalogue:E-catalogue/hard copy of catalogue
Website: www.bq-medical.com/www.bqplusmedical.com These 2 IP links to same website.
Email: info@bq-medical.com
Web pic:
Q2Is BQ+ a reliable manufacturer of medical products?
Ans
BQ+ has the following certificates and registrations of the infusion sets or components:
Certificates pic:
Supplier Audit is essential to become qualified suppliers of big Medical groups. We passed every audit ever since, here are some examples of Audit reports..
Certificates pic:
Q3What information do I need to provide to help BQ+ partners understand my needs?
Ans
Would you please let us know the following:
-Basic information about your company?
-What you are buying this product for?
-Annual purchase quantityof iv sets or components?
-When would you like to start this project?
Q4May I ask for samples? May I use samples on patients?
Ans
Yes, of course.
-In order to save time for both of us, please first communicate with our sales representatives about the specific product specifications, configuration, technical requirements, packaging requirements and so on. We will make samples to demonstrate our understanding of your requests, and for your lab testing. We could share our test protocols and results from BQ+ lab for your reference.
Q5How does BQ+ ensure the safety of product?
Ans
BQ+ highly respects medical law and regulations,
-Medical grade materials are used for components injection molding and tubing extrusion.
-DEHP Free, PVC free, Latex Free, BPA free materials are widely used in BQ+ products.
-MSDS reports, biocompatibility test reports are available.
-Technical Data Sheet, accelerated aging report, real-time aging report are all available.
-Package validation report for individual packaging, such as peel pouch and blister packing.
-For sterile products, EO Sterile validation report will be provided.
-All products shipped are provided with COC and COA
Q6How are the products packaged?
Ans
- Individual Pack
-Peel Pouch, Blister pack (soft & hard blister) are commonly used for good sterilization effect.
- Inner pack
-Boxes and PE bags are commonly used. Qty per pack varies from products.
- Outer carton
-Strong 5 - ply corrugated cartons suitable for long distance transportation.
- Pallet & Container
-We make pallets for LCL and wrap them with wrapping film.
-Containers are generally not palletized for thepurpose of making the best use of container contents. If you have special request, we can also make pallets for your container cargoes.
- Individual Pack
BQ+ Medical Quality
Q1How does BQ+ guarantee the quality?
Ans
- Planning
-Before the formal mass production of BQ products, according to the requirements of laws and regulations and the necessary design and development process, the product's material, structure, intended use, performance indicators and other technical requirements as well as the production process are designed and verified, and the relevant technical documents are issued through the quality management system and implemented.
- In-Process Quality Control
-BQ+ implements Total Quality Management. Products in the production process, including material feeding, injection molding, extrusion, assembly, bonding, packaging, sterilization and inspection all links, there are corresponding production records and inspection records, each process is in accordance with the corresponding drawings, operating procedures, inspection procedures and other technical documents for operation. Keep a detailed record of the traceability information of each project, the operation content and technical parameters of each process, and the inspection results of each technical requirement.
-Total Quality Management is also reflected in the quality awareness and training level of all staff. BQ+ production and inspection personnel must undergo corresponding skill training and pass the examination before they officially take up their posts.
- How does BQ+ guarantee the quality?
-The non-conforming products in the production process shall be confirmed by the quality personnel or reviewed by the responsible departments according to the document requirements and shall be repaired, reworked,
-scrapped and other disposal measures to ensure that all products meet the quality requirements.
-Each customer feedback and complaint case will be carefully investigated and actions taken. BQ+ quality engineers on complaint handling and CAPA ability will ensure a smooth cooperation with every clients.
- Improvement
-We promise a safe usage of BQ+ products by devote our sustained engagement in continuous improvement. Not only the improvement identified by our own QMS, but also the chances of improvement from our treasured clients. Every voice from you will be appreciated and considered as a valuable source of our improvement!
- Planning
Q2Could BQ+ do EO sterilization?
Ans
BQ+ possesses an independent Ethylene Oxide Sterilization Center besides its production lines. The sterilization validaiton and routine contorl procedures have been well established according to ENISO11135 standard and additional local requirements from China FDA.
As ENISO13485/ENISO11135 certificates holder, We are supervised by routine audit of notified body TUV Rheinland and also the national authority CFDA.
We also accept audit from domestic and foreign customers. Our service on process validaiton ranks top level in China and we provid routine sterilization service for hundreds of enterprises both domestic and abroad of China.
BQ+ provides sterile products which meets EN556-1 defination on sterility, with a SAL=10-6.At the same time, BQ+ also provides commercial EO sterilization service aimed at lower down bioburden or product disinfection.
Our quality is assured with ISO13485 quality management system and traceability is well established. Each sterilization Service with be provided with the following documents:
-Sterilization batch record
-Sterilization certificate
-Results of BI culture
-EO residue test result
Q3How is the logistics and storage of BQ+ controled?
Ans
BQ has set up a special warehouse to store all raw materials and products. The warehouse is equipped with pest control facilities and the environment temperature is monitored.
The warehouse implements partition management for raw materials and finished products. Place raw materials or finished products according to their respective product names, specifications, models, etc., and register the traceability information of raw materials and products such as product names and batch Numbers through identification cards. The warehouse keeps information for incoming and outgoing materials and products, and carries out dynamic management.
All products shall be inspected by quality personnel and confirmed to be qualified before being put into storage. The warehouse arranges the delivery according to the shipping instructions of the sales department.
Q4How does BQ+ ensure product traceability?
Ans
In the whole process of infusion set or IV components production, BQ identifies and records raw materials, semi-finished products and products to ensure that the product status and source of raw materials can be identified and traced from the whole process of material in-coming, production, inspection and delivery.
We have the order #, raw materials code & Lot #, product code, lot #, quantity, production/test equipment, equipment operation parameters, sterilization lot #, sterilization parameters, test results, disposal of non-conforming product information such as records, and confirmed by the corresponding management personnel, ensure record fill in accurately and timely.
After the production of a certain batch of products is completed, all production and inspection records shall be uniformly filed into the batch records of that batch, which shall be checked by the personnel of the quality department and then filed to the document control department of BQ company for safekeeping.
After the delivery of products, if there are any abnormalities or complaints, we can trace the product code, batch number and other information back to the batch records, repeat the production process, and investigate and analyze the causes of abnormalities.
Q5How do I know the order status and quality level before shipment?
Ans
BQ+ sales team is base in factory, and they keep interaction with production, quality and logistic team. They are following your medical device order status and quality controlling, in case there is any issue, you will know it immediately.
BQ+ sales representative will send you photos/videos to keep you posted.
FQC will be done before releasing goods from BQ+ factory, COC/COA will be issued by BQ+ laboratory. You could do “remote video inspection before shipment” and see container loading through sales representative’s mobile phone camera.
Q6What if there quality issues after I received the shipment?
Ans
Don't worry, BQ+ Guarantees:
Sales responds in 24hours Investigation in 3 days
Proposal of Compensation in 7 days
Corrective and preventive action plan in 30 days
CAPA close in 90 days.
The following support needed from your side:Please do inspections within 30 days after shipment arrives.If there is any quality issue,
It is helpful to provide photos or videos.
Please describe the scenario as detailed as possible.
Please provide your inspection result, test method and sampling standard.
Please let us know the current disposition status of the problem products.
- Tel:
86-021-57743953
- Address:
- No.18,Cheye Road,Songjiang District,Shanghai 201611 China.
- Email:
- info@bq-medical.com
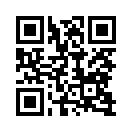